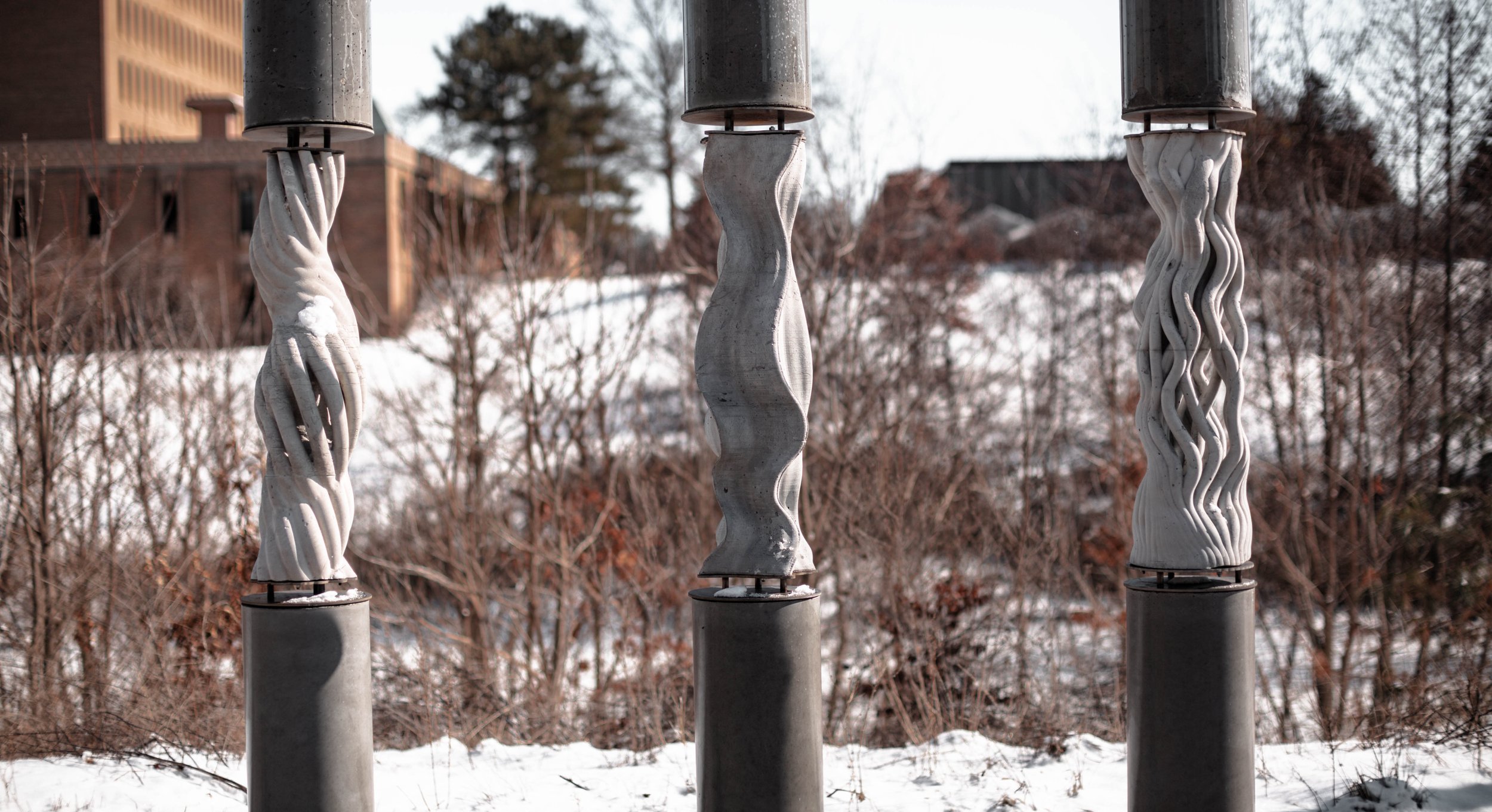
The degree of geometric complexity a concrete element can assume is directly linked to our ability to fabricate its formwork. Additive manufacturing allows fabrication of freeform formwork and expands the design possibilities for concrete elements
The performance of 3D printed formwork and its geometric complexity varies, depending on the type of plastic used for 3D printing the formwork and the printing technology. The three columns showcase the degree of geometric freedom achievable in concrete formwork when printing with different materials—namely PLA, PVA, and PETG—and using different 3D printing techniques—robotic fused granulate fabrication (FGF) and fused filament fabrication (FFF) cartesian machines.
PLA (Polylactic Acid) is a common plastic material in the 3D printing industry, being both biodegradable and produced from renewable, organic starches. PVA (Polyvinyl Acetate) is a water-soluble synthetic polymer often used for support material on complex 3D prints due to its ease of removal when in direct contact with water. This research uses PVA to directly 3D print the formwork parts. Due to its high sensitivity to moisture, PVA requires airtight storage. Because of the material’s sensitivity, PVA can clog the nozzle of a 3d printer. PETG (Polyethylene Terephthalate Glycol) is a thermoplastic copolyester with high chemical resistance, durability, and ductility. It is also fully recyclable.
3D printing plastic formwork can transform concrete construction and enable the production of individual freeform concrete structures quickly and cost-effectively, minimizing construction waste and labor. The degree of geometric complexity a concrete element can assume is directly linked to our ability to fabricate its formwork. Additive manufacturing can facilitate complex freeform geometries and expanded design solutions for concrete elements. In particular, fused filament fabrication (FFF) 3D printing of thermoplastic, which is used to produce the formwork of the columns, is a useful method of fabrication due to the lightweight properties of the resulting formwork and the accessibility of FFF 3D printing technology. The design and fabrication of the three concrete columns exhibited investigates PLA, PVA, PETG, and the combination of PLA-PVA as a formwork material.
Through an entirely digitized design-to-production workflow for concrete formwork, 3D printing allows the integration of all functions that are needed in a concrete element. The columns showcase the additive manufacturing, enabling the prefabrication of large-scale, lightweight, and ready-to-cast freeform formwork to minimize material waste, labor, and errors in the construction process while increasing the speed of production and economic viability of casting non-standard concrete elements.
THINSHELL PLASTIC FORMWORK
This research seeks to achieve formal complexity in concrete by cross-referencing and investigating PLA, PVA, and PETG print materials, as well as a combination of PLA-PVA formwork. PLA (polylactic acid) is a common plastic material in the 3D printing industry, being both biodegradable and produced from renewable organic starches. PVA (polyvinyl acetate) is a water-soluble synthetic polymer often used for support material on complex 3D prints due to its ease of removal when in direct contact with water. This research uses PVA to directly 3D print the formwork parts. Due to its high sensitivity to moisture, PVA requires airtight storage containers, and because of the material's sensitivity, PLA can clog the nozzle if it is left slightly hot or cold when not extruding. PETG (polyethylene terephthalate glycol) is a thermoplastic copolyester with high chemical resistance, durability, and ductility. It is also fully recyclable. This research hypothesizes that combinatory additive manufacturing of multimaterial formwork as a new approach will expand the geometric freedom of formwork in an economical manner.
Initial fabrication understanding diagrams
DESIGN QUESTION
“How can architects redesign the modern column with omage to the historical charateristics of the past?”
PROCESS
Our research found that PVA caan be difficult to work and develop. To midigate ony of the issuse that my arise we decided to start small and fine tune the material setting until comfortable. (right) A small scale study that yeilded successful results from printing to casting to formwork removal. (bottom) was the result of fine-tuning the setting to sacle the prints larger allowing for scaling to the 1:1 column.
FDM Printing of PVA and Computing of the Inner Voids The second column expands on existing research into water-soluble formwork by examining the performance of large-scale PVA formwork (1 m height) and strategically combining PVA and PLA prints into a single formwork. PVA dissolves in a high-moisture environment therefore, a formwork application enabled new design features for concrete elements with complex geometry, including inner voids, undercuts, long tubular voids, and deep hollow areas. However, the print speed of PVA was limited to ensure proper layer adhesion and required careful moisture control. By combining PVA and PLA, PVA was selectively applied to locations of geometric complexity and later washed away. The remainder of the formwork was printed in PLA, where formwork removal was not a constraint.
The multimaterial formwork consists of one PVA and two PLA parts, printed using 1.75 mm diameter filament. The PVA filament required special considerations to prevent it from reacting with the water content present in the air, thus degrading the quality of the filament by producing air pockets in the material. This issue was mitigated by providing a controlled printing environment using desiccant and an airtight enclosure to dehumidify the material sealed inside. Also, the initial PVA printing tests did not properly adhere to the printing bed. This was resolved with a textured tape placed on the bed, an increased first layer extrusion rate (150%) and a decreased print speed (35 mm/s).
Print time was a major consideration in the production of the formwork. To accelerate the printing process, the print was split into PVA and PLA material sections, because printing with PLA is faster than PVA for the same geometry. The 640 mm high PLA parts were printed in 26h20m and the 360 mm high PVA part was printed in 37h30m. The design of the geometry evolved along with material experimentation. PVA allowed for easy removal of formwork with undercuts and pockets, while the removal of the PLA was much more challenging and cumbersome with these features. Although PVA was initially chosen for its desirable water-soluble properties to ease the formwork removal, the first test showed that the water content in the concrete mixture weakens the structural performance of the PVA formwork. The wall thickness in this early prototype consisted of 2 shells with 0.4 mm width for each shell (0.8 mm in total). Because the PVA formwork would be exposed to a much higher moisture content in the full-scale cast, an additional layer was added to the shell, making the wall 1.2 mm thick.