A lightweight façade system can significantly reduce greenhouse gas emissions resulting from construction. Lightweight building envelopes can take less time to install, require less scaffolding, use less energy for transportation, and reduce the overall weight of the building, resulting in a lighter foundation. This project presents Topology Optimization as a design method that, in combination with 3D printing, allows for the manufacturing of materially efficient, geometrically complex building envelopes. The project focused on production of a lightweight, yet strong building envelope based on wind and gravity loads. This promotes a shift from planar cladding to systems which integrate form as both membrane and structure. Beyond material optimization, the project highlights the potential of a multidisciplinary design methodology for building envelopes which takes advantage of the capabilities of 3D printing.
Topology optimization strategies concentrate material in areas where structural loads are the highest, and this often results in bone-like, branching structures which produce discrete “islands” of material when sliced into layers for the printing process. One of the known challenges in large scale fused pellet manufacturing (FPM) is the difficulty of precisely starting and stopping the extrusion process. This project makes significant advances in this area through the development of tool-path strategies as well as hardware control paradigms which improve the fidelity of the final printed part.
Bounding box dimensions of part 1: approx. 2440 by 620 by 50 mm (height X width X depth), 10 mm mm thickness of the thin shell
Bounding dimensions of part 2: approx. 2440 by 1220 by 50 mm (height X width X depth), 10 mm mm thickness of the thin shell
Material: thermoplastic PETG
Volume of Material: 35.4 litter
Panel Weight: 38.2 Kg
Printing time: 44 for part one and 23 hours for part two
Number of mesh faces: 100,000
Toolpath kilometer in panel: 8,848 meters
Topology Optimization for Building Envelope
Modern, high-performance building envelopes require the integration of numerous functions within a discrete, panelized construction system. This research began with a question: “Can additive manufacturing (AM) improve the performance of a building envelope by allowing for the enhanced integration of diverse goals such as light transmission, insulation, thermal mass, natural ventilation, and structure?” One of the key capabilities of AM is its ability to produce topologically complex forms. Topology is a branch of mathematics that is concerned with how the geometric properties of a shape are affected by continuous transformations. Famous examples include the Möbius strip and Klein bottle. By controlling the connectivity of internal passages and layers, this building envelope provides enhanced thermal performance while allowing light transmission and reducing the need for inefficient glazing systems.
In the prototype presented here, two topological regions are created. One connects an inner void with the outside and inside of the façade through apertures, and the other connects the inner void of the outer layer and inner layer. The outer surface is corrugated through a “reaction diffusion” algorithm, producing rib-like stiffeners which enhance the structural stability of the outer surface. Future work in this area will investigate the addition of translucent insulation materials like silica gel, as well as phase change materials (PCM) for energy storage. These materials can be placed within the envelope according to solar gain in interconnected passages which allow for efficient thermal transfer.
Dimensions of each panel: approx. 2270 by 1170 by 200 to 230 mm (height X width X depth), 8 to 50 mm thickness of the outer layers
Material: thermoplastic PETG
Volume of material for one panel: 41.3 liters of polymer
Weight of one panel: 44.5 kilograms
Printing time of each panel: 44 hours
Number of mesh faces in the low-resolution panel: 70,000
Number of mesh faces in the high-resolution panel: 840,000
Toolpath kilometer in low resolution panel: 10,323 meters
Toolpath kilometer in high resolution panel: 10,333 meters
Multilayer and Functionally Integrated Building Envelope Project
Acknowledgement for 3D Printing Concrete Formwork Project
Project Instructor: Assistant Professor Dr. Mania Aghaei Meibodi
Contributing researchers:
Ryan Craney, Christopher Voltl
Contributing Students: Ryan Craney, Han-Yuan Chang, Monik Gada, Feras Nour, Christopher Voltl, Jessica Lin, Chia-Ching Yen, Carl Uwe Eppinger, Aaron Weaver
Funding Support: Master of Science Digital and Material Technologies Program.
Acknowledgement for Topology Optimization for Building Envelope Project
Project Instructors: Assistant Professor Dr. Mania Aghaei Meibodi and Associate Professor Wes McGee
Contributing researchers:
Christopher Voltl
Contributing Students: Mackenzie Bruce, Gabby Clune, Chris Humphrey, Ben Lawson, Colleen Ludwig, Sarah Nail, Mehdi Shirvani, Ruxin Xie.
Funding Support: Master of Science Digital and Material Technologies Program.
Acknowledgement for Multilayer and Functionally Integrated Building Envelope Project
Principal investigators:
Mania Aghaei Meibodi, Assistant Professor, Taubman College of Architecture and Urban Planning, University of Michigan. Director, Digital Architecture Research and Technologies Laboratory.
Wes Mcgee, Associate Professor, Taubman College of Architecture and Urban Planning, University of Michigan. Partner, Matter Design.
Contributing researchers:
Alireza Bayramvand, Christopher Voltl, Ruxin Xie
Funding Support: Taubman College of Architecture and Urban Planning Research and Creative Practice seed fund.
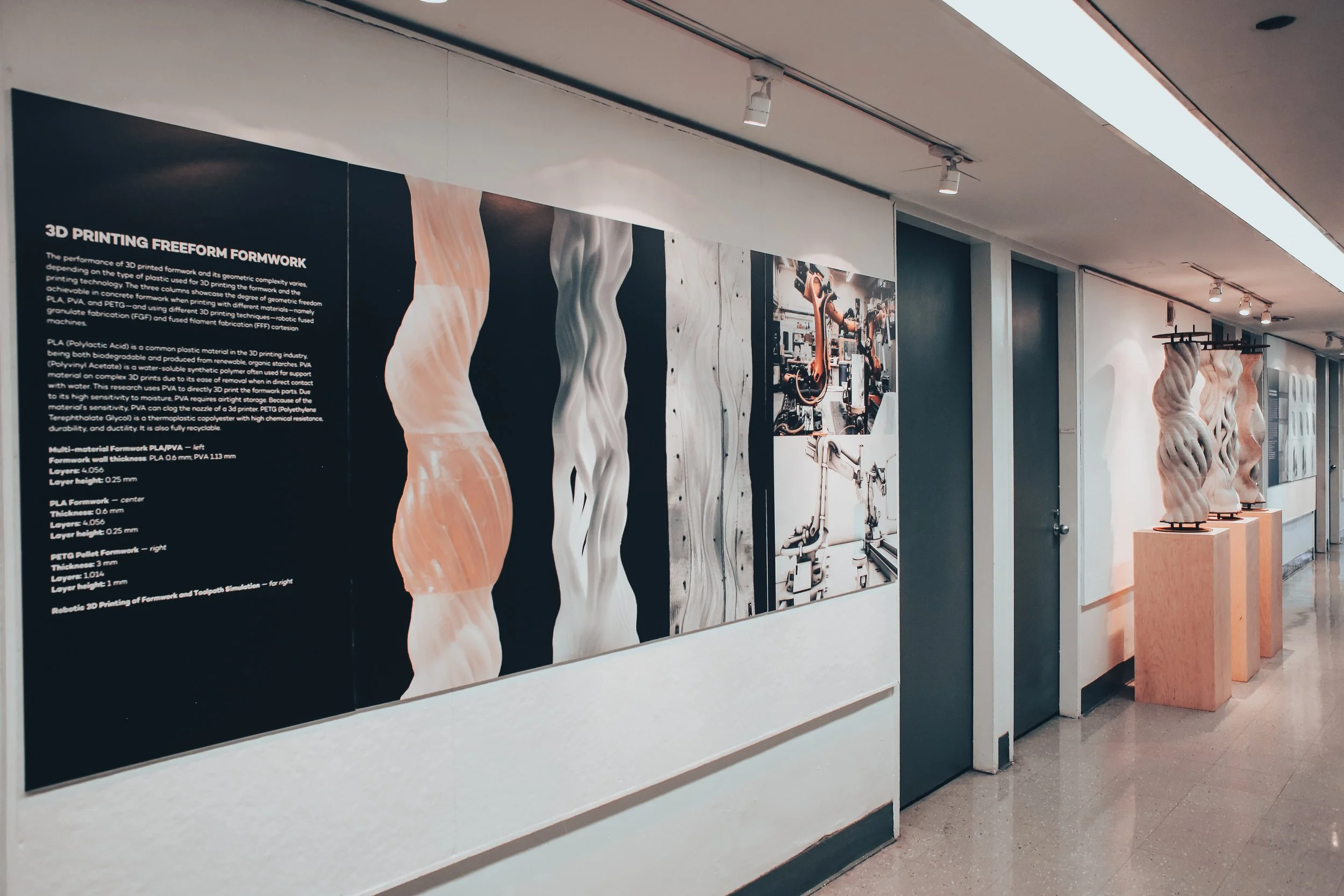
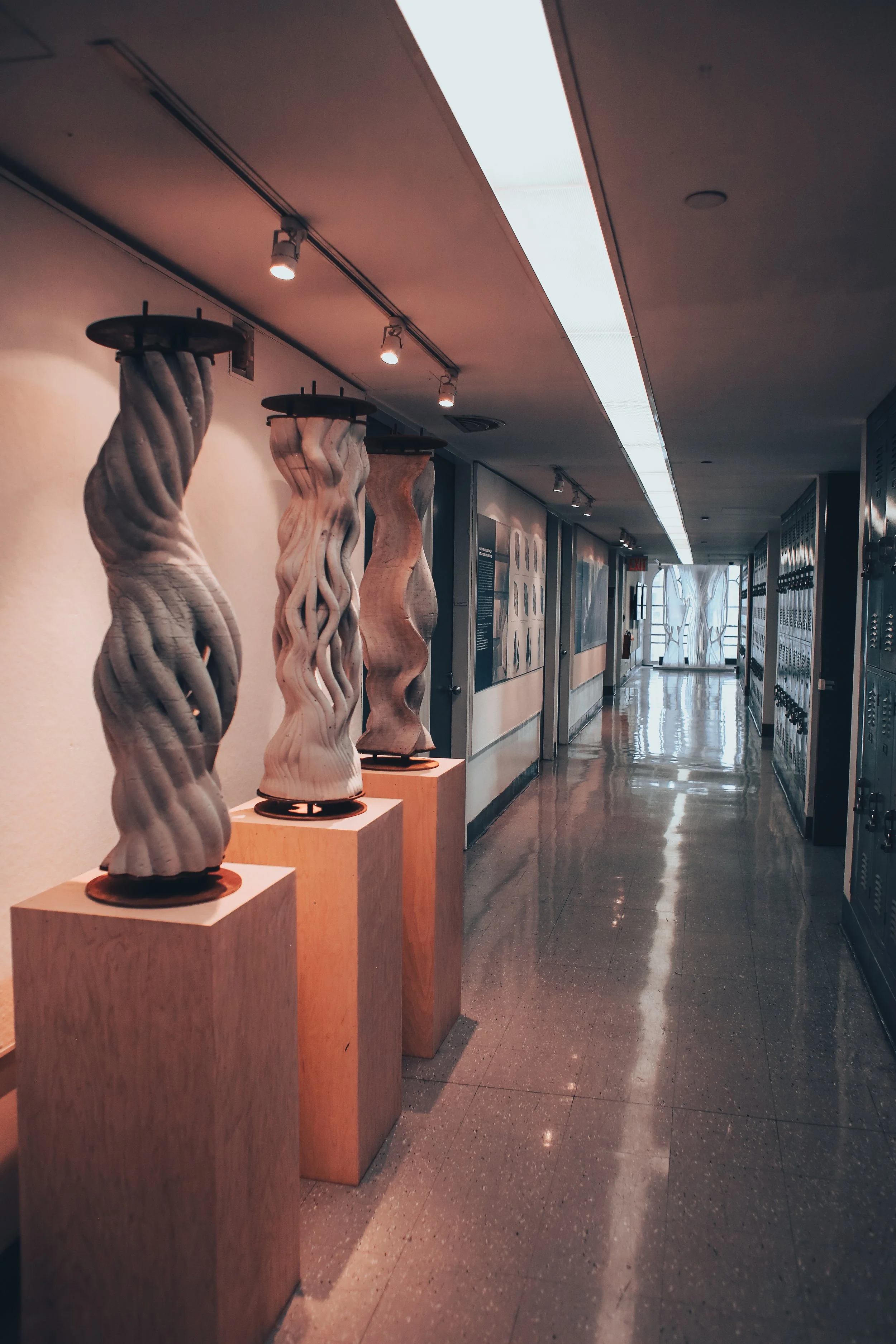
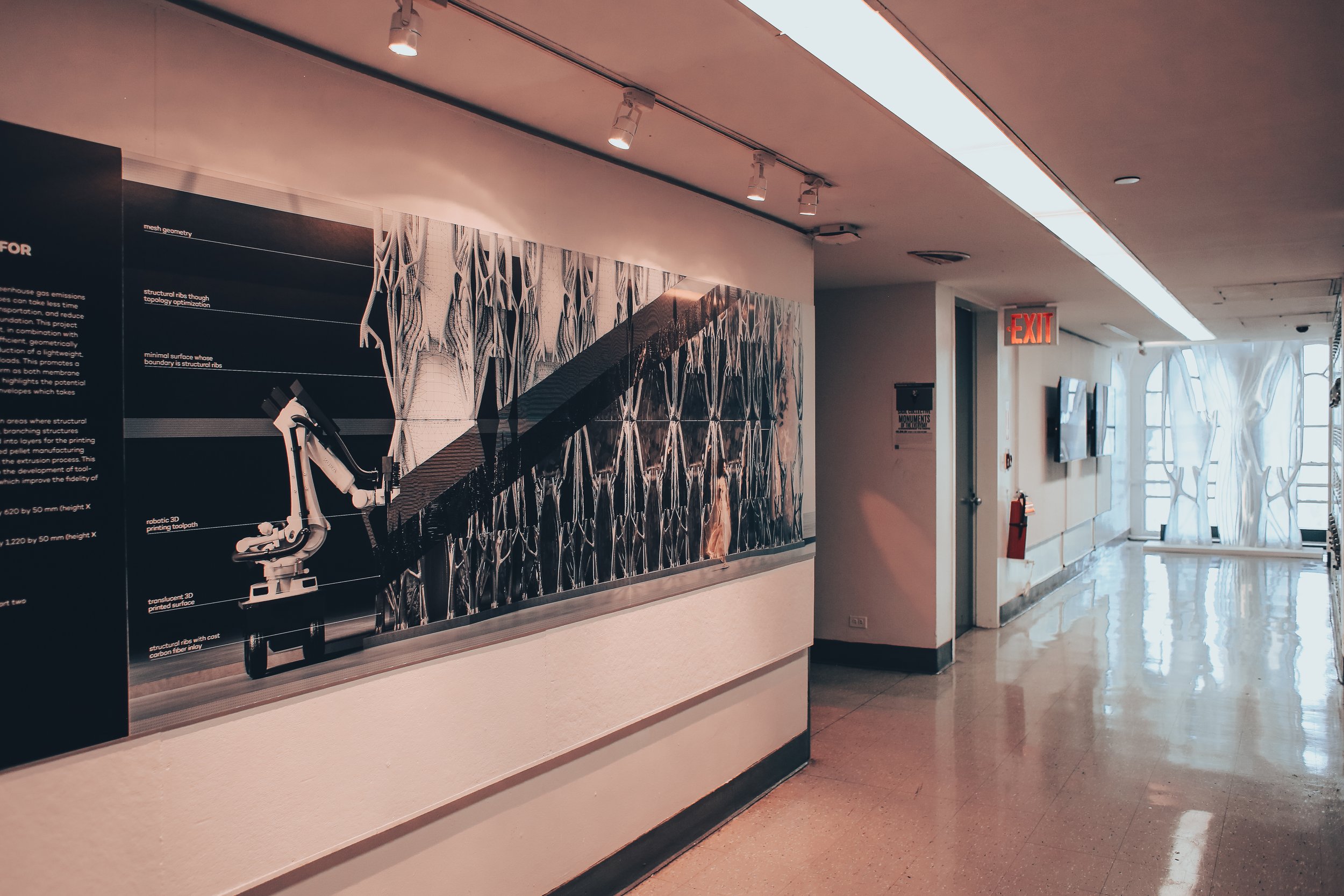
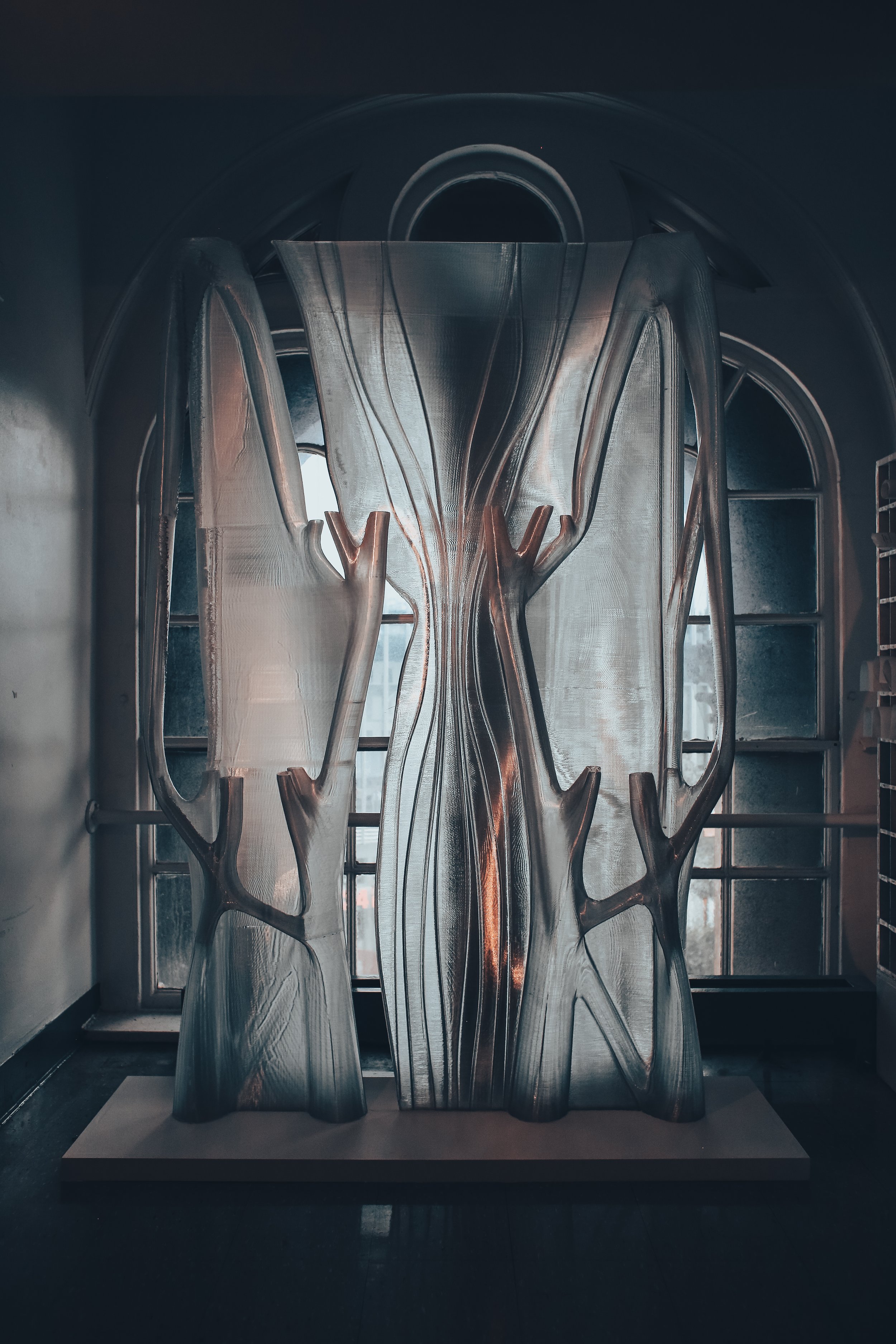
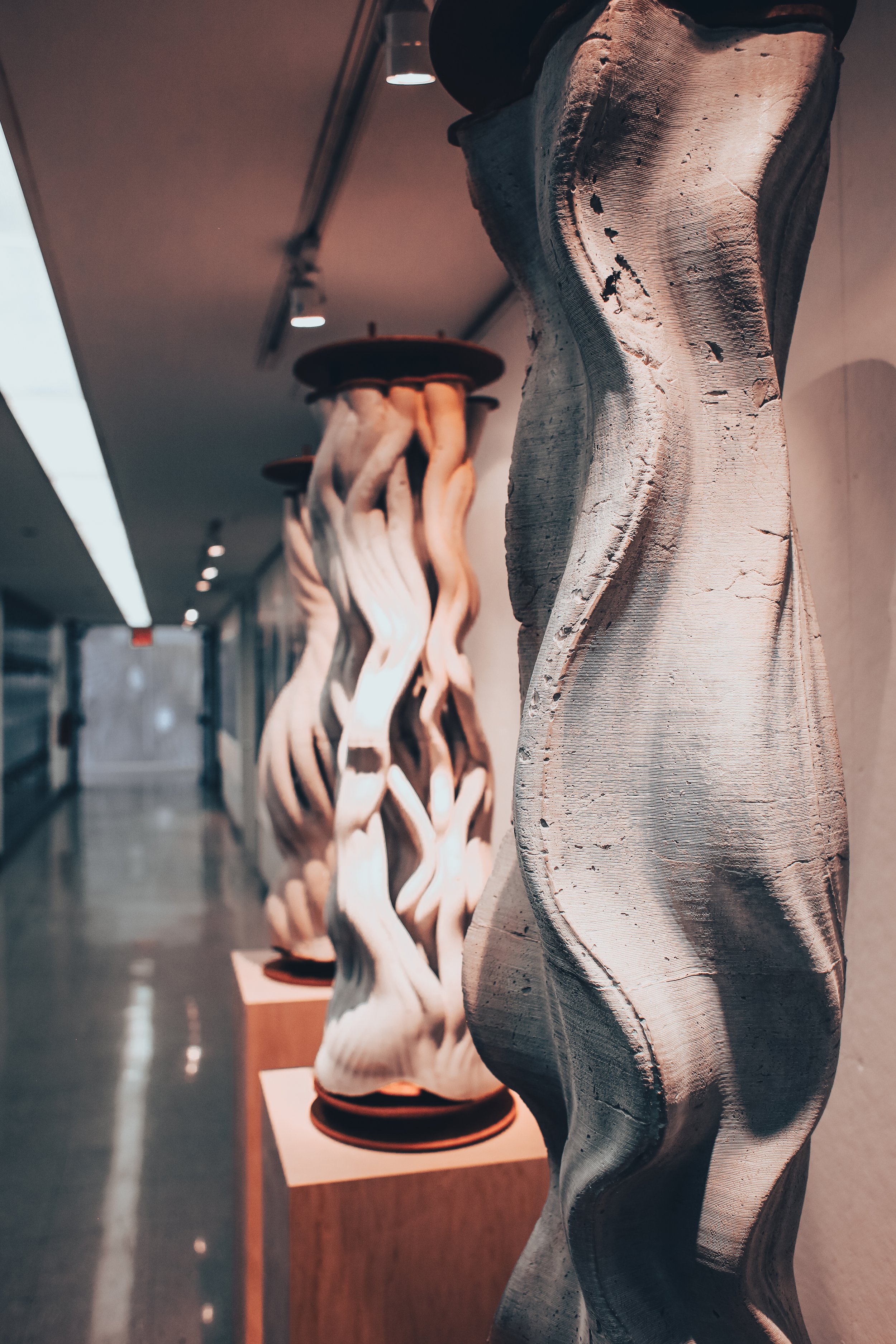

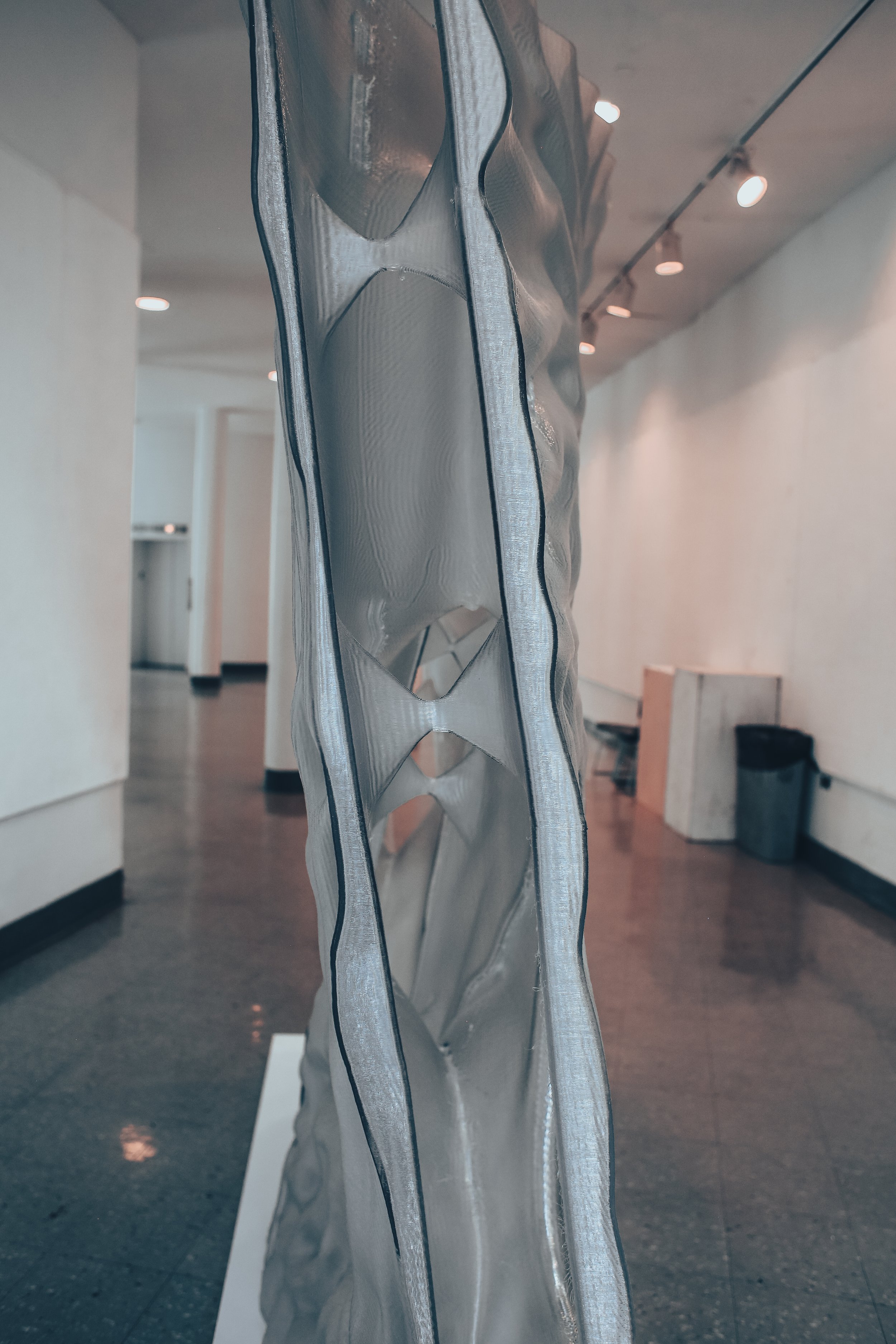

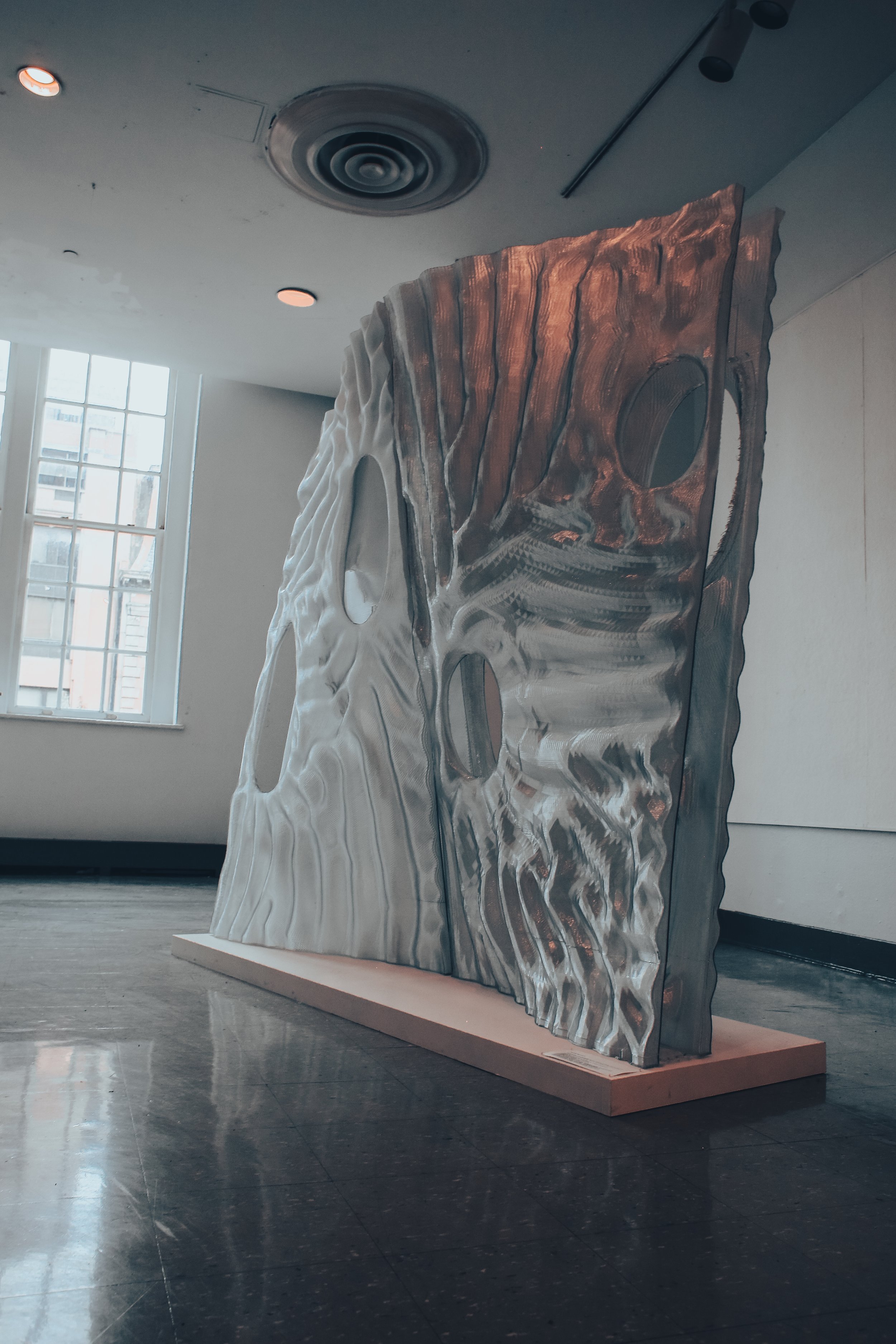